Managing Risk or Ignoring It? A Public Works Case Study
- Gail Birks
- Feb 25
- 3 min read

In a recent engagement we gave "flipping the switch" a new meaning with a public works organization.
The Lean Performance Improvement (Kaizen) Teams at a municipal public works agency partnered with CMA to examine their Risk Management protocols and culture. The end goal being a safer and more accountable workplace. While this was part of their Lean Certification Journey for a Green Belt Project Certification in Lean Six Sigma, the results established a threshold for achieving this desired quest for sustainable success.
Shortfalls like avoidable mishaps, poor messaging, unclear Standard Operating Procedures (SOPs), or ignored monitoring and accountability were discovered. These issues raise questions like:
Why does this keep happening?
Who owns this process or performance issue?
What monitoring and follow-up are needed to ensure safety?
Have we considered that fear of losing paid work time or jobs may cause underreporting of injuries?
How are we tracking our success… or not?
Here is a snapshot of some insights and transformations adopted by the organization.
The Issue - Risk Management to Manage or Not:
A Subject Matter Expert (SME) Team assembled to investigate the assumption that a more refined reporting process will lead to the reduction in reporting errors and incidents. More important, City wide safety awareness, efficient investigations and the overall reduction in financial settlements for worker’s compensation cases. There will also be verification and validation of appropriate training and competency enhancements, or not for the targeted areas.
The focus was on the “Why” with regard to excessive workers’ compensation claims and missed workdays. The team discovered claims were filed when injuries that could no longer be ignored and/or often times were repeat incidents. Staff admitted they didn’t know how or when to complete forms, and supervisors overlooked minor injuries to maintain a skeleton crew in place. Adequate staffing was stressed to reduce absenteeism and injuries.
The primary issue is that there existed a culture of complacency and status quo. Specifically, in spite of the current state, neither leadership nor the workforce felt that there was an issue to the current incident rates being reported.
Key areas noted from initial investigations included:
Lack of incident reporting due to insufficient communication and training on “how to” report occurrences.
Lack of proper investigation after an occurrence
Safety policies need to be improved
Absence of consistent enforcement for required and necessary PPAAE
Requirement for older facilities to receive upgraded infrastructure
Reported incident rate of 7.89
Sigma Level of 1.18
More Senior Level Management engagement is needed
Absence of sufficient data to benchmark performance administratively and in the field offices. The SME Team data reflected a Goodness of Fit of 21% compared to a threshold of 80% which is deemed acceptable
Training needs for workforce have not been clearly identified
Cost of Poor Quality was estimated as $1239.97 per incident/failure or roughly 20 times a year
Insufficient Staffing Levels:
SME Team members expressed a greater need for organization leadership to improve staffing levels in the field service areas. At the time of the project, staff levels in the field offices were 285. Based on their assessment, using the CMA Toolkit, required staff levels were estimated to be 316, a difference of 31 positions. This could probably help to reduce the attrition rate and absenteeism rate of 16.42 and 3.24% respectively.
Rework, Redundancy and Wait time:
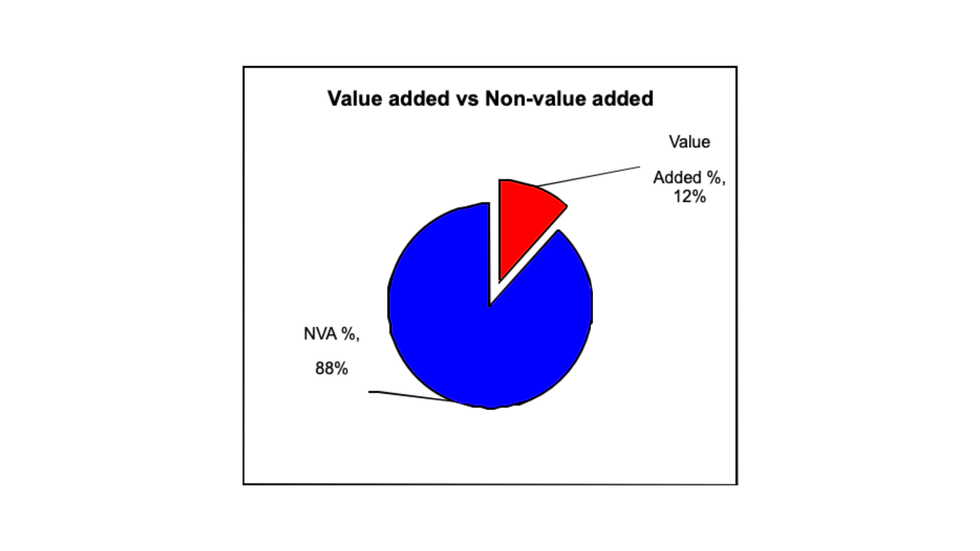
The Non-Value/Value-Added tool made it clear that there is quite a bit of Non‐value added time in the incident reporting process. For the samples reviewed, reports are sometimes incomplete, filled out improperly and not seen by the appropriate individuals. There are also instances where employees are not reporting until several days later when the injury becomes a problem. This leads to an increase in non‐value added time, specifically waiting.
Recommendations:
Staff training and online reinforcements were created to ensure understanding of safety and wellness expectations. Our coaches facilitated a shift for team members, helping them work through lessons learned. This team successfully rallied stakeholders to support their recommendations.
Utilizing the performance metrics developed by the team to assess efficiency, effectiveness and that safety policies are being implemented consistently.
Other outcomes include:
New communication channels to ensure accountability and proper monitoring
Heightened morale and workforce confidence. While this was not included in the scope, by creating a safe and more educated workforce, improved morale becomes the bonus
Clarified and scoped training requirements.
Clearly defined monitoring metrics and consistent accountability reporting
For more information on scheduling your Lean Journey, contact Gail Birks at 954-476-3525, email: info@cma-ent.com or visit cma-ent.com.
Comments